When working with wrought iron, a big decision is whether or not to galvanize it. Galvanizing protects wrought iron from rust and corrosion, making it a more durable and long-lasting option. This guide will explain everything you need to know about galvanized wrought iron, including what it is, why it matters, and how it can enhance your projects.
What Is Galvanized Wrought Iron?
Galvanized wrought iron is wrought iron that has been coated with a protective layer of zinc. This process, called galvanization, prevents rust and corrosion by creating a barrier between the iron and the environment.
There are two primary methods of galvanization:
- Hot-Dip Galvanizing: The wrought iron is dipped into a bath of molten zinc, coating every surface.
- Electrogalvanizing: A thinner layer of zinc is applied using an electrochemical process.
Hot-dip galvanizing is the most common method for wrought iron, as it provides superior protection.
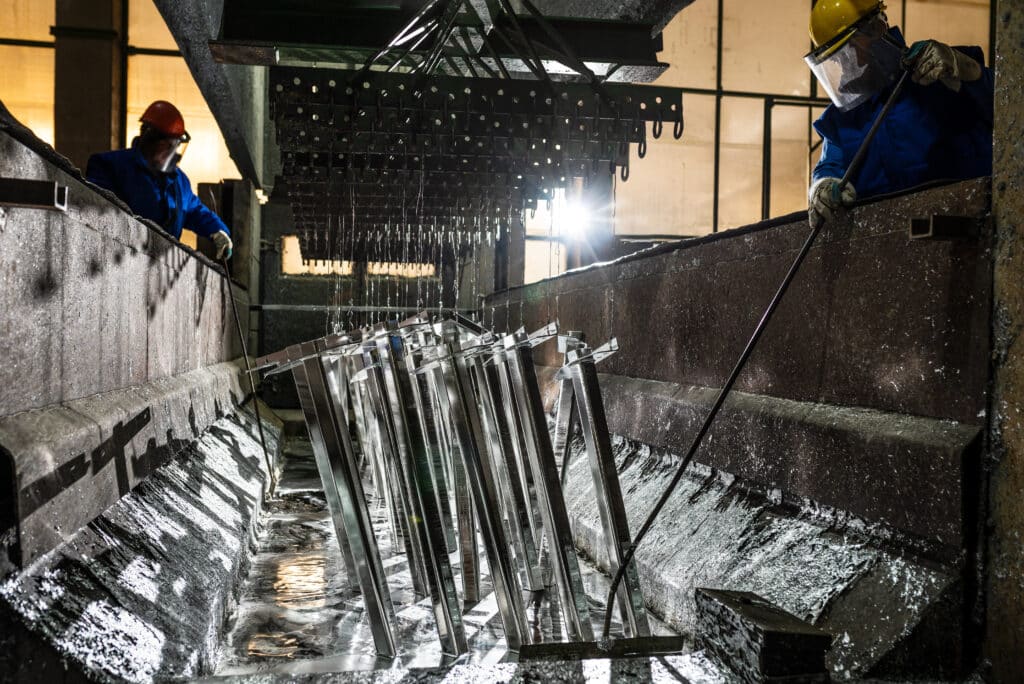
Benefits of Galvanizing Wrought Iron
Galvanizing wrought iron comes with several advantages that make it an excellent choice for outdoor and indoor projects. Let’s break them down:
1. Rust and Corrosion Resistance
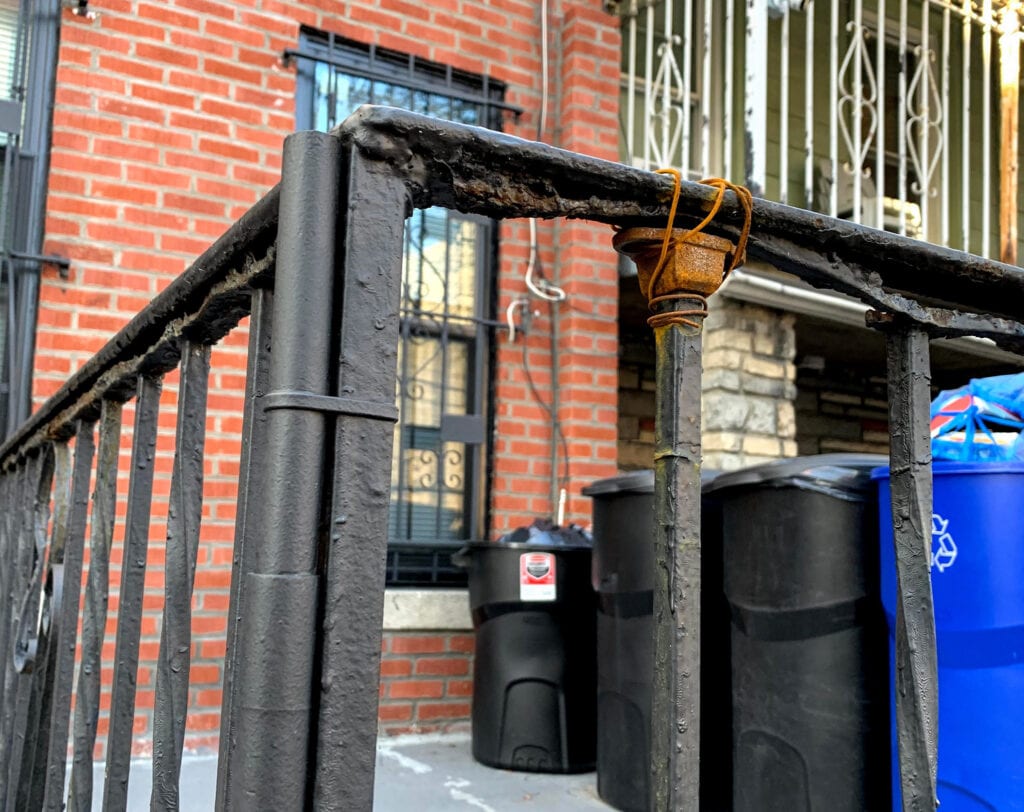
The zinc coating acts as a shield, preventing moisture and oxygen from reaching the iron. This is especially important for outdoor applications where exposure to rain, snow, and humidity can cause unprotected wrought iron to rust.
2. Longer Lifespan
Galvanizing can help your work last decades with minimal maintenance. The zinc coating extends the life of the iron by preventing wear and tear caused by the elements.
3. Cost-Effectiveness
While galvanizing adds an upfront cost, it reduces long-term maintenance expenses. Repainting and repairing rusted iron can add up over time. Galvanizing minimizes the need for these fixes.
4. Aesthetic Appeal
The shiny finish of freshly galvanized wrought iron can be visually appealing. Over time, the zinc develops a matte patina, which many people find attractive.
5. Environmental Benefits
Galvanized wrought iron is eco-friendly. Its durability means fewer replacements, reducing waste. Zinc is also recyclable, further lowering its environmental impact.
When Should You Choose Galvanized Wrought Iron?
Galvanized wrought iron is ideal for projects exposed to harsh conditions. Here are some examples where it shines:
Outdoor Fences and Gates
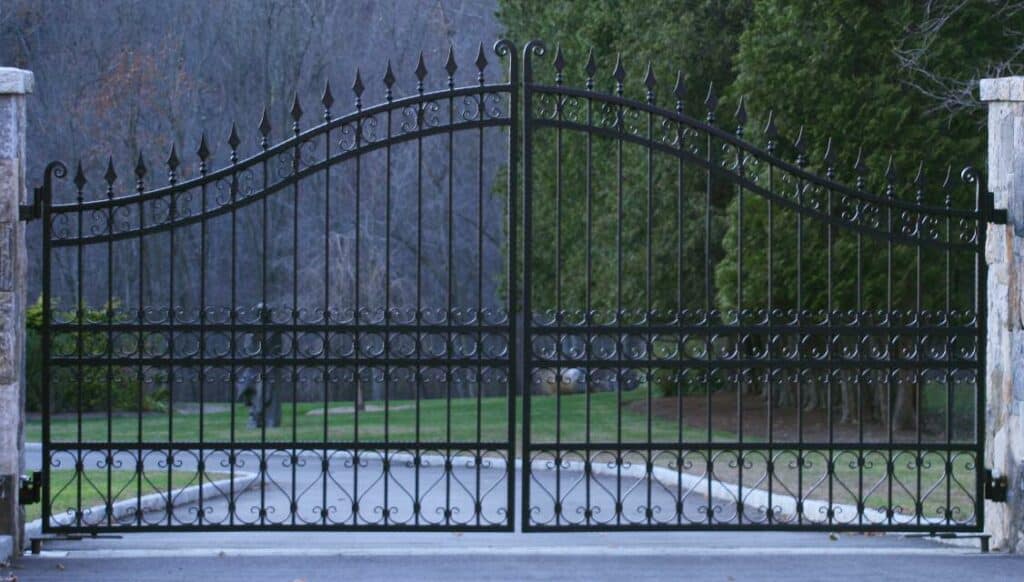
Outdoor wrought iron structures face constant exposure to the elements. Galvanizing ensures these pieces remain sturdy and rust-free for years.
Railings and Balconies
For railings, especially those near the ocean or in humid climates, galvanizing prevents salt and moisture from causing corrosion.
Structural Supports
Wrought iron beams and supports benefit from galvanizing in industrial or residential settings, particularly where moisture is present.
Decorative Items
Even decorative items like planters and trellises can benefit from galvanizing, as it preserves their look and structural integrity.
How Is Iron Galvanized?
The galvanization process is relatively straightforward but requires expertise to ensure proper application. Here’s an overview:
1. Cleaning the Iron
The wrought iron is cleaned to remove dirt, oil, and rust. This step is critical to ensure the zinc adheres properly.
2. Flux Application
A chemical flux is applied to the clean surface to prepare it for galvanizing. This prevents oxidation during the process.
3. Hot-Dip Galvanizing
The wrought iron is submerged in molten zinc, coating it entirely. The zinc bonds to the surface and forms a protective layer. For more details about the galvanizing process and its standards, visit the American Galvanizers Association.
4. Cooling and Inspection
After galvanizing, the iron is cooled and inspected for any missed areas or imperfections.
5. Optional Finishing
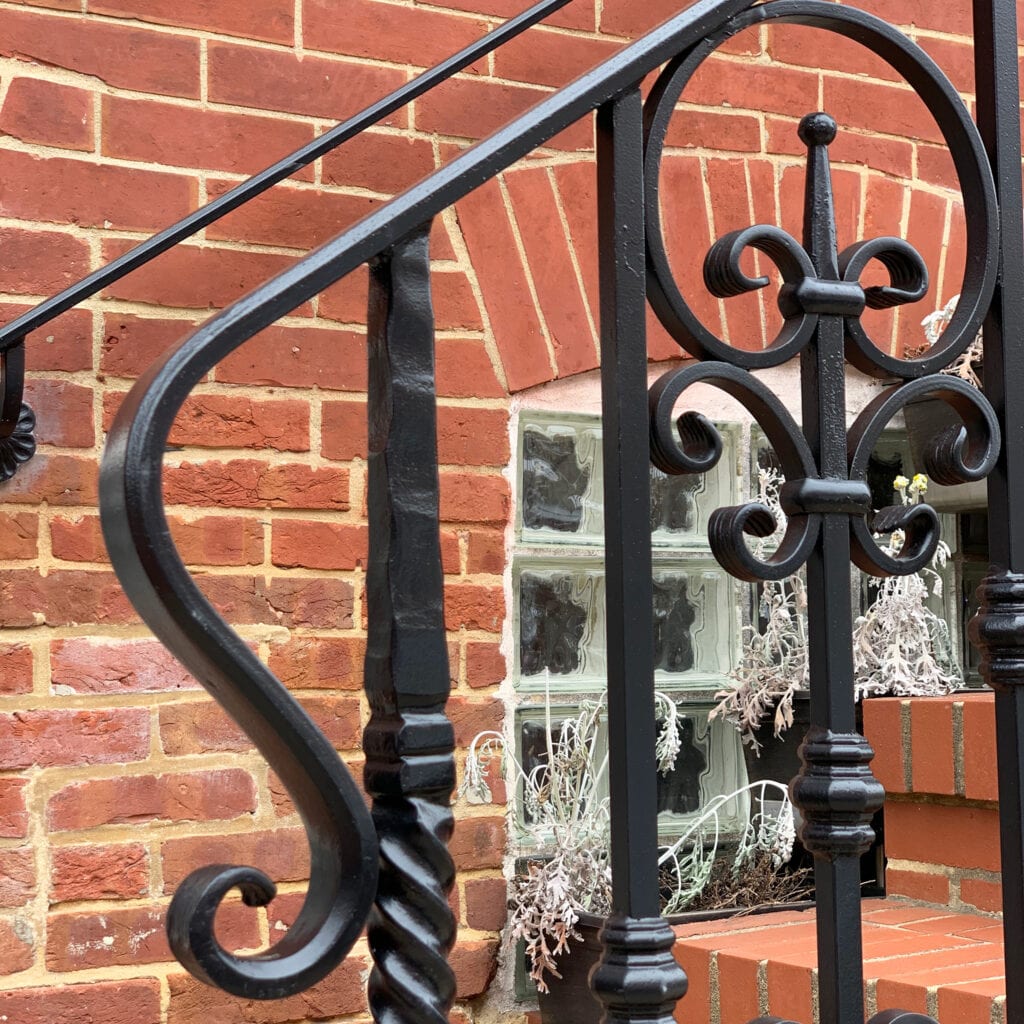
For certain projects, a powder-coated finish can be applied over the zinc for additional protection and aesthetic purposes.
Common Concerns About Galvanizing
While galvanizing offers many benefits, some concerns are worth addressing:
1. Upfront Cost
Galvanizing does add to the initial cost of a project. However, the long-term savings on maintenance often outweigh this.
2. Appearance
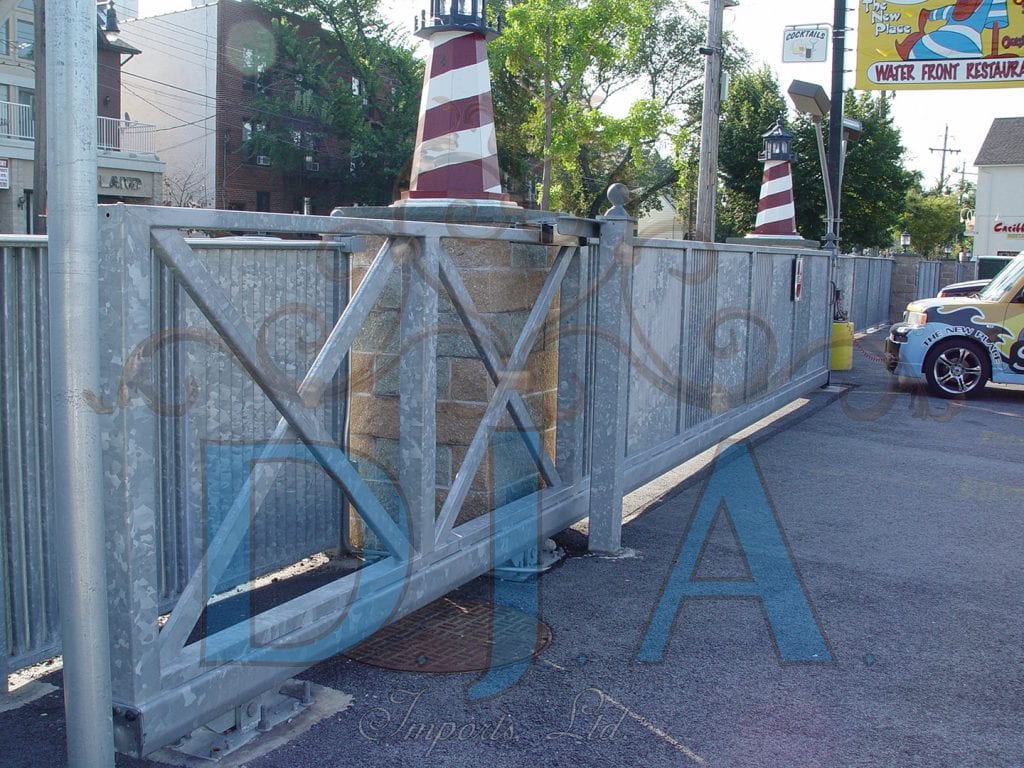
Not everyone likes the look of galvanized wrought iron, especially if they prefer the raw iron aesthetic. Painting over the zinc layer is an option for those seeking a different finish.
3. Potential Warping
During hot-dip galvanizing, the high temperatures can sometimes warp intricate ironwork. Experienced professionals can minimize this risk.
Maintenance Tips for Galvanized Wrought Iron
Although galvanized wrought iron requires less upkeep than untreated iron, some maintenance ensures its longevity:
Clean Regularly
Use soap and water to clean dirt and debris from the surface. Avoid abrasive cleaners that could scratch the zinc coating.
Inspect for Damage
Check for any scratches or chips in the zinc coating, as these can expose the iron to rust.
Recoat If Necessary
In rare cases where the zinc coating wears thin, additional galvanizing or a zinc-rich paint can restore protection.
Avoid Harsh Chemicals
Chemicals like acid or chlorine can damage the zinc layer. Use mild cleaning solutions for best results.
Why Choose Galvanized Wrought Iron for Your Next Project?
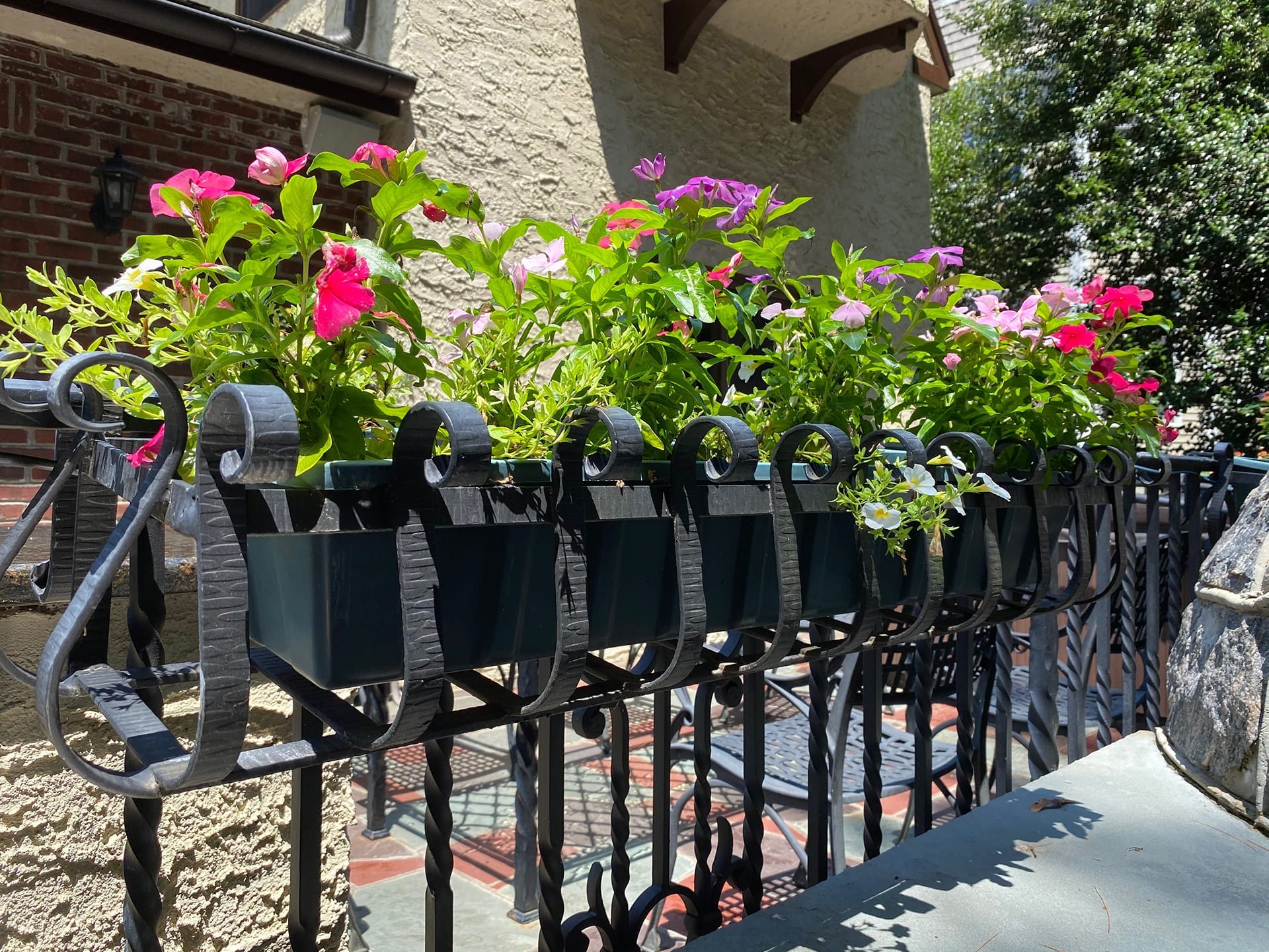
Galvanized wrought iron combines strength, durability, and aesthetic appeal. It’s an investment in the longevity of your project and reduces the need for constant maintenance. Whether you’re installing a fence, a gate, or an industrial support structure, galvanizing ensures your wrought iron will stand the test of time.
Fabrication Tips
In general, we recommend hot dipped galvanizing for any exterior metalwork project that uses steel or cast iron components. Based on our decades of fabrication experience in both residential and commercial settings, here are some tips we’ve compiled to help ensure your project is a success:
1. Drill Holes in Enclosed Assemblies
Tubes, fully-enclosed caprails, and channel assemblies need small, drilled holes to allow molten zinc to flow freely. This ensures full coverage inside and out. Always consult your local galvanizer for specific guidelines.
2. Use Thicker Materials to Avoid Warping
The high heat of the zinc bath can cause thinner materials to warp. Use ¼” or thicker solid plates, especially for structural elements like bottom plates in gate fabrications. This precaution helps maintain the integrity of the design. (See below for a gate photo example.)
3. Galvanize Steel and Cast Iron Separately
Steel and cast iron have different optimal galvanizing temperatures. To avoid complications, galvanize them separately and then mechanically fasten them together for the best results.
4. Ensure Professional-Quality Welds
High-quality, professional welds are essential for a smooth and durable finish after galvanizing. Poorly executed welds can create weak points and aesthetic flaws.
5. Plan for Galvanizer-Specific Requirements
Preparation work and job minimums may be required by your local galvanizer. These can include cleaning, pre-treatment, or ensuring parts meet specific size or design criteria. Check with your galvanizer early in the planning process.
6. Consider Zinc Bath Size Limitations
The size of the zinc bath at your local galvanizer determines the maximum dimensions of a single section. These limits range from 10 feet to 40 feet depending on the facility. Larger sections also require stronger materials to prevent warping. For oversized pieces, consider metalizing as an alternative.
7. Use Stainless Steel Fasteners
For long-lasting results, incorporate stainless steel fasteners throughout your project. They resist corrosion and work well with galvanized materials.
8. Post-Galvanizing Finishing Is Often Required
Some finishing work, such as removing drips or smoothing surfaces, is typical after galvanizing. Use a worn sanding disk to clean up edges without damaging the zinc layer.
9. Avoid Galvanizing for Ultra-Smooth Finishes
Hot-dip galvanizing is not recommended for applications where an ultra-smooth surface is critical, such as entry doors or decorative elements. In such cases, alternative coatings or finishes may be better suited.
By following these guidelines, fabricators can design and produce wrought iron projects that withstand the test of time. For additional fabrication tips and expert advice, consult your local galvanizer or visit the American Galvanizers Association.
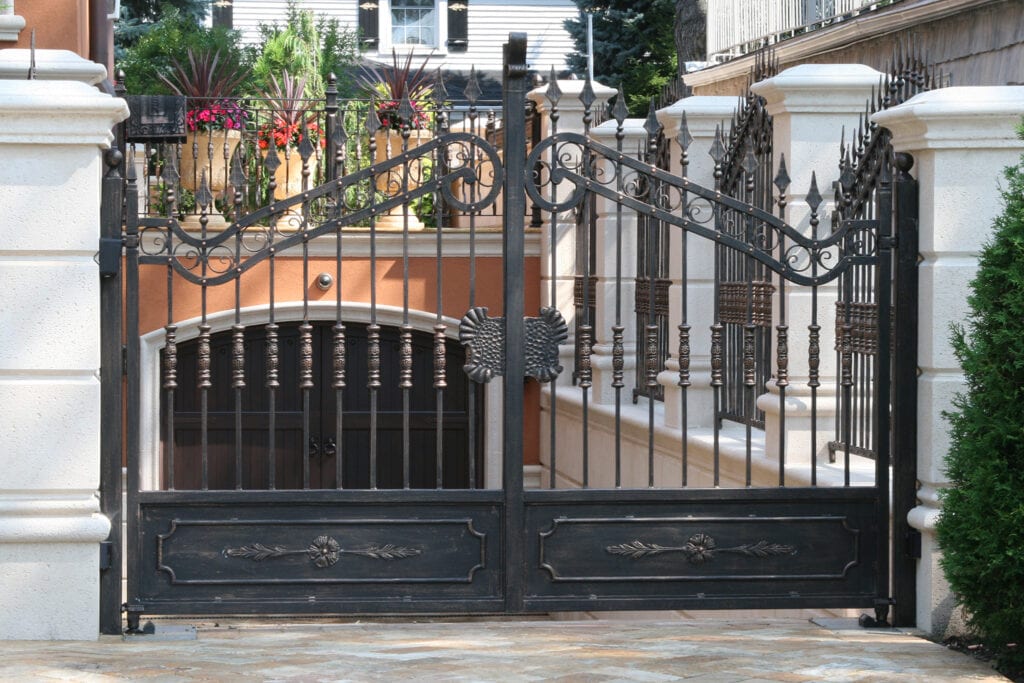
Choosing galvanized wrought iron is a smart decision for anyone looking to create durable and attractive structures. It protects your investment from rust and corrosion, ensuring it lasts for decades. Whether you’re working on a backyard fence or a commercial project, galvanized wrought iron is a reliable and cost-effective solution.
By understanding the benefits, process, and maintenance of galvanized wrought iron, you can make informed decisions for your projects. When you’re ready to start, trust experts who specialize in wrought iron and galvanizing to deliver the best results.
Frequently Asked Questions
How long does galvanized wrought iron last?
Galvanized wrought iron can last 50 years or more when properly maintained. Its zinc coating provides durable protection against rust and corrosion, even in harsh environments.
Can you paint galvanized wrought iron?
Yes, galvanized wrought iron can be painted, but proper preparation is essential. Use a primer designed for galvanized metal to ensure the paint adheres effectively.
Is galvanizing environmentally friendly?
Galvanizing is an eco-friendly process because it extends the lifespan of wrought iron, reducing waste. Additionally, zinc is fully recyclable, further minimizing environmental impact.
Does galvanizing protect against all types of corrosion?
While galvanizing provides excellent protection against rust, it may not prevent corrosion from extreme chemical exposure. For specialized environments, additional coatings may be required.
Can I galvanize wrought iron myself?
DIY galvanizing kits are available, but the process can be challenging for large or intricate projects. Professional galvanizing ensures a high-quality and durable finish.